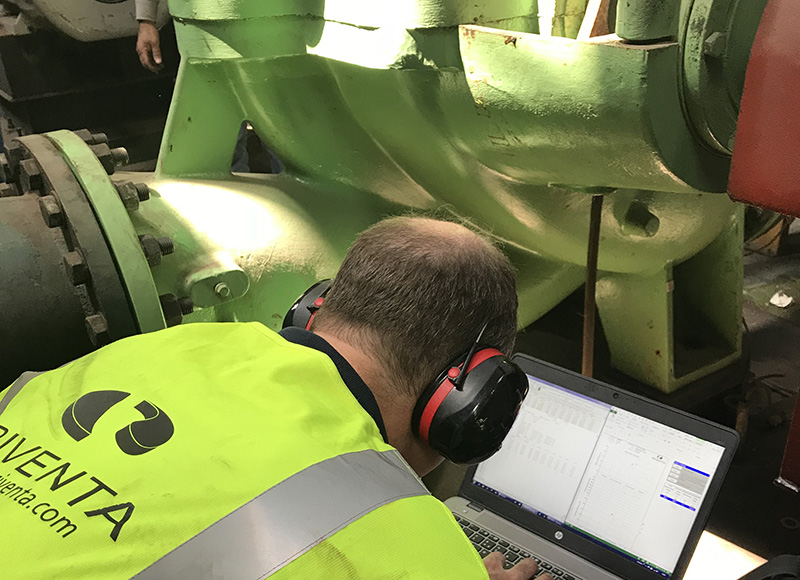
At a Sao Paulo pumping station, we directly measured the efficiency of three 700CV (515kW) water distribution pumps using our FREEFLOW portable thermodynamic pump testing system.
Eighteen months on, our client has seen very significant improvements. Our pump rescheduling recommendations led to immediate savings; while the least efficient pump we measured was removed and refurbished.
Post-refurbishment, the cleaned-up pump now exceeds the manufacturer’s expectations, running at over 80% – a 53% improvement! As a result, savings of more than 13% out of the 15% we forecasted are now being realised, with further refurbishment measures on other pumps (and related savings) still yet to be implemented.
Get your copy of our updated case study Pump efficiency testing in Brazil – including a new section on ‘What happened next?’
Building a strong reputation in Brazil
One of our strengths is undoubtedly the close relationships we’ve developed with in-country partners. As a network, we continue to seek opportunities and new clients.
Our work in the country is gathering pace – and we’re moving from just consultancy work to more equipment installations.
Here are just two examples of our consultancy work:
Water treatment on the Rio Negro
In the city of Manaus – on the Rio Negro just before its confluence with the Amazon, 1,100km from the coast – one of our partners, Improv Equipamentos, was provided with a brief by a large water treatment plant, with approx. R$16m/year ($4m/year) energy cost for pumping, to find the best and most easily realisable energy saving opportunities. We provided the specialist pump testing equipment and hydraulic engineering knowledge, and a prioritised course of action to yield the greatest return on investment. We also provided the plant with a sound operational basis to improve pump longevity and optimise efficiency.
In total, 23 pumps were tested across the water treatment plant that contains two separate parallel abstraction and treatment processes, which each then pump potable water into distribution.
There were many unique factors to consider. For example, water abstraction is hydraulically complicated by an 11m increase in river level in winter from 18m in the summer, increasing static head by 60%. As well as this, the black sediment that gives the Rio Negro its name, increases abrasive wear. Therefore, accurate efficiency measurement has revealed the pumps in the best and worst hydraulic condition. We found, depending on the pumping combination used, efficiencies that varied from 47% to 81%.
With the identification of the pumps in poorest repair, we have helped the client to prioritise the refurbishment works, which in terms of the vertical turbine pumps (515kW rating), is a very expensive and complex undertaking (approx. R$300,000/pump for all on-site extraction/installation and off-site refurbishment works). More efficient operation and better pump selection does not just mean lower energy costs, but moreover it extends Mean Time Between Repairs (MTBR) thus reducing the frequency of these very resource hungry events.
In all cases we advised how to operate most efficiently and in a way that mitigates wear rate in future and accommodates the very dynamic hydraulic conditions.
Back in Sao Paulo…
As an example of the application of our technology in industry, we’re using our portable FREEFLOW equipment to run comparison tests for a private company that takes treated effluent from one of the largest sewage treatment works in South America and post-processes it. Using ultra filtration, it produces a high purity water for sale to industrial processes downstream (e.g. for boiler feed water and high-quality process water), which is substantially cheaper for them relative to local ‘towns water’ and removes any additional abstraction burden.
The programme of work involves us testing the company’s pumps (3 x 660kW, 128m, 375l/s) and making recommendations regarding refurbishment work. Once refurbished, we then re-test pumps to verify outcomes, which in general will provide:
- Ability to confirm the decision for remedial works to internal stakeholders
- Verify magnitude of expected energy savings through increased hydraulic efficiency
- Evidence to hold refurbishment contractor to account and/or justify any contractual bonus or penalty payment in connection with it
The recommended pump refurbishments completed so far have resulted in performance exceeding the manufacturer’s ‘as-new’ expectations. The most recent refurbishment has increased hydraulic efficiency from 76% to 86%, reducing specific pumping costs by 11%. This was attributed to good refurbishment practice but also the addition of low-friction coatings to the hydraulic surfaces. The investment made for the remedial works, including the very marginal expense to discover and confirm the opportunity, will be paid back in <2.5 years.
It greatly benefits the owner to know confidently both how efficiently his energy is being consumed and to understand the health of their assets.
Get in touch:
As with our work across Brazil, we’re confident our approach and the technology we use will identify savings and efficiencies in your pumping plant. If you feel we can help, please do get in contact ›