Safety, reliability, and efficiency are top priorities for the petrochemical industry. Our Optimised pumping solutions will achieve significant reductions in energy and emissions, boost performance and reliability.
Choose your petro- chemical application:

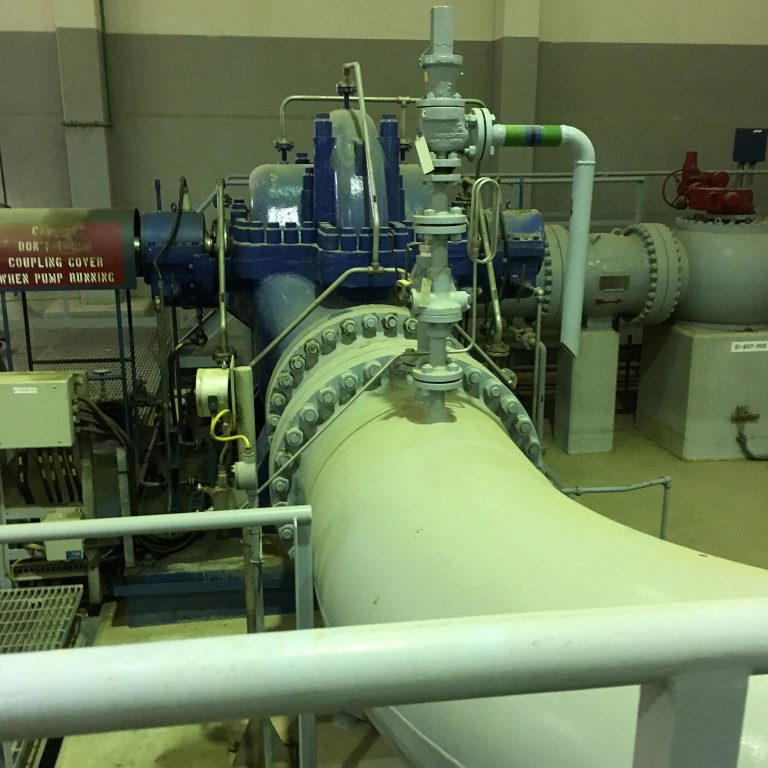
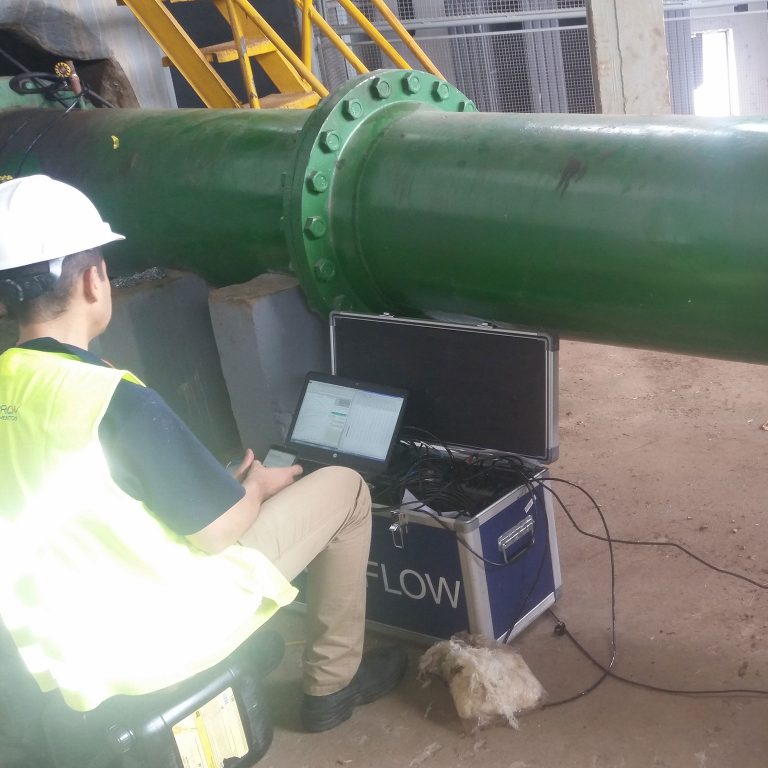
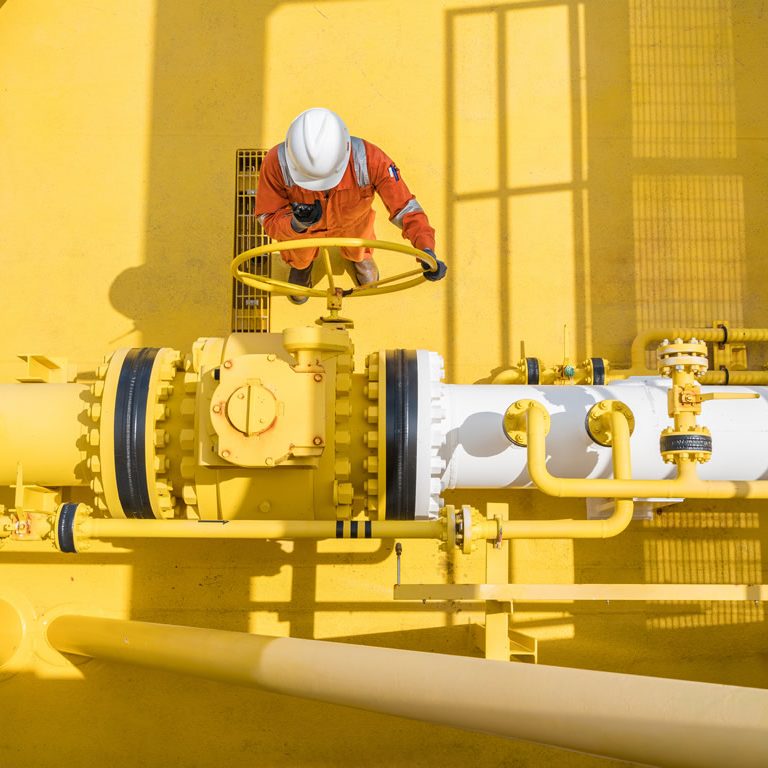
Want to discuss how our solutions can help you?
Call us on +44 (0) 1872 260005 or click here to get in touch