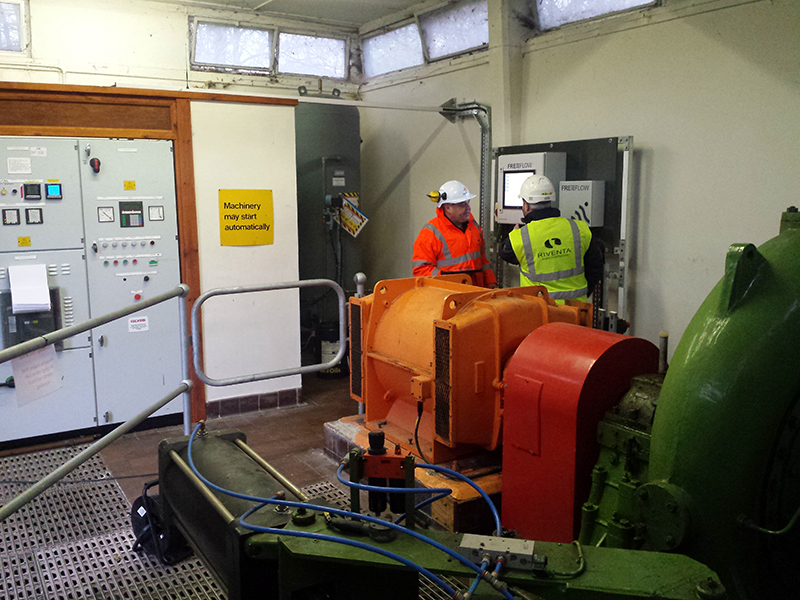
The hydro-turbine is a fixed speed machine (1016rpm) that runs without any human intervention, with its load controlled via flow rate modulation using inlet guide vanes.
Why efficiency monitoring?
From a simplistic viewpoint, the effectiveness of a pumping system is defined by:
- The correct specification of operating performance criterion for the duty (how close to BEP is it running for much of the time?)
- A maintenance strategy that reflects the degree of difficulty to manage (how worn is it and since when?)
- Use of the best available technology (are there better and more affordable assets available to achieve the same thing?)
How was the turbine optimised?
Our FREEFLOW monitoring equipment was installed on the hydro-turbine. Alongside our client, we then looked at how to operate the turbine for the best return within the operational constraints of the overall network. So, we:
- Observed and analysed the turbine’s current hydraulic characteristics, building a picture of how it operated and when.
- Offered steps to improve its performance by adjusting the way the sub-network was controlled. Here, we minimised the use of guide-vanes and maximised opportunities when the turbine could run, allowing a greater proportion of time spent at BEP.
- Determined what newer technologies exist or the refurbishment options that would provide an economically justifiable improvement beyond the turbine’s original performance expectations (currently, best hydraulic efficiency achieved = 82%).
How were efficiencies found?
FREEFLOW was able to immediately highlight whether scheduling changes were effective or not. In doing so, it provided real-time tracking of any savings associated with a specific change, enabling us to optimise the turbine’s operations.
For example, while the turbine operated at an annualised average hydraulic efficiency of 73%, if increased to 80% this would translate to at least £11,000 per year savings, based on little or no capital investment.
Next steps
Our long-standing partnership with this UK water company means we are continuing to investigate the turbine’s performance.
Get a copy of our case study:
The above has been extracted from a fuller case study, which you can request by clicking the following link: Turbine efficiency monitoring in the UK